Sponsored Sessions
Continental Automotive Sibiu, a Diamond Sponsor of ESTC 2022, has organized some special sessions to present and discuss latest developments in automotive electronics.
ACCESS TO THOSE SPONSORED SESSIONS IS FREE FOR ALL CONFRENCE ATTENDEES!
Sponsored Session 1 - Development of Electronic Braking Systems for Harsh Environment
Eugen Craciun, Hardware Project Leader, Vehicle Dynamics
Mircea David, Mechanical Design Team Leader, Vehicle Dynamics
Valentin Bujor, Hardware Group Leader, Vehicle Dynamics
Within this workshop, we want to present how we develop the electronics and mechanics for a braking system assuring that the interconnection is suitable for the harsh environment. From initial customer request to a robust product on the street there are several milestones: concept, design of electronics and mechanics, validation and successfully launch the product
We will have a live demo showing the interconnection between electronics and mechanics as well how the simulation environment for validation is looking like.
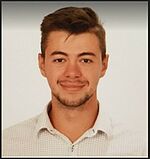
Hi! My name is Eugen and I have been working in Continental for over 8 years.
In the beginning I worked for Transmission Department, as Hardware Developer for e-Bike projects. For the last 6 years, I have been part of the Vehicle Dynamics department, starting as Hardware Test Engineer and now I am Hardware Project Leader for Brake and Suspension Systems.
I am mainly responsible for driving, managing, and monitoring all the Electronics Related Activities within a specified time, ensuring product quality and customer satisfaction.
Planning, Customer Requirements Review, Qualification Alignment, and Project Tracking are the most essential day-to-day activities.
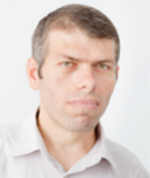
Hi! My name is Mircea and I’ve joined into Continental’s family in 2009, 13 years ago, in the Electronic Braking Systems Department in the Mechanical Design Team. Since then, as mechanical designer at the beginning, technical project leader after a while and team leader today, I've been involved in very interesting projects, most of them being already strategical in our braking systems portfolio.
During all these years, I had the chance to learn many new things about the "mechanics behind the braking system's ECUs". Our responsibility as a team is to meet customer's requirements by developing new solutions starting from the concept phase till the series production support the complete life cycle of the Electronics and its components: housing, cover, PCB, coils etc.
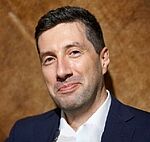
Hi! My name is Valentin and I have been working in Continental for more than 11 years.
I have started my journey in the Electronic Braking System as a “Hardware Test Engineer” where I had the chance to work with a dedicated team and learn the amazing insights of the electronic testing system, safety features and the outstanding development for a safe driving experience in the car.
From test engineer to my current position of Hardware Group Leader I had also the opportunity to gain additional abilities as failure analysis, test specification development and team leading for the testing team.
My role today is to provide a flawless test management for the brake and suspension system prototypes developed in Continental and to optimize and use the latest technologies close to our setup development.
Sponsored Session 2 - Qualification Laboratory - Vibrations in Automotive
Oana Lia Lascu
Tiberiu Baldogi
The Qualification Laboratory (QL) Sibiu is recognized by customers providing benchmark for product validations and related services.
Reliability testing is performed to ensure that the Device Under Tests is reliable, it satisfies the purpose for which it is made, for a specified amount of time in a given environment and is capable of rendering a fault-free operation.
Environmental and mechanical testing conducted to simulate hazards that can affect the longevity of a product in a controlled, repeatable and accelerated fashion. This will help identify failure modes, so they can be addressed and verified as solved during the product development cycle.
For Reliability area we can perform tests as follow: Temperature, Climatic, Intrusion Protection, Corrosive, Mechanical, Vibration, Electrical tests and Visual/Thermal inspection.
Tests performed to determine any mechanical weaknesses (breakage) and/or degradation of performance (malfunctions) due to fatigue (accumulated stress effects).
Additional resonance tests with laser vibrometer are considered in order to determine critical resonance frequencies and then undertake an endurance test at resonance frequencies for a prescribed time.
Electromagnetic compatibility (EMC) is the branch of electrical engineering concerned with the unintentional generation, propagation and reception of electromagnetic energy which may cause unwanted effects such as electromagnetic interference or even physical damage in operational equipment.
EMC is composing from two major parts: Emissions, Susceptibility and Immunity.
We are an essential part of Continental Automotive Quality and contribute to our business' success by excellent test services throughout the entire PLC (Product Life Cycle).
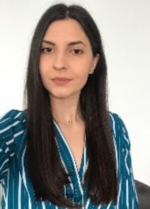
Hello, my name is Oana and I have been working at Continental Sibiu since 2018. I started as a Validation Engineer in Qualification Laboratory and became Team Leader of the Validation team in 2020. Me and my team are in charge of connecting and collaborating with our customers and are always ready to offer support in order to provide our services in a respectable and highly-regarded manner.
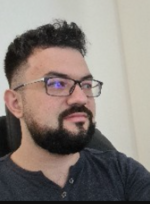
Hi, my name is Tiberiu!
I am a Vibration Test specialist at Continental!
My journey with Continental started 7 years ago when I joined an interesting department called Qualification Laboratory. Since then I learned a lot about this field and not only. I learned how important correct measurements are, by appreciating the uncertainty, I learned how automobile components are designed to withstand all sorts of environmental conditions, and many more!
Sponsored Session 3 - From Innovation to Standardization: The journey towards robust manufacturing solutions
Laura Boarescu
Lucian Rusu
Dinu-Tudor Gruian
Sergiu Andrici
This workshop will describe how to facilitate innovation, accelerate standardization through know-how exchange and develop generic robust manufacturing solutions in a global high-volume, automotive electronics manufacturing environment via technical networks.
In today's electronics manufacturing environment, we are faced with component shortages, increased complexity of the products, but continuously diminishing production costs and higher quality levels. Therefore, innovation is a key element for more efficient manufacturing technologies that need to be deployed as soon as possible to adapt to an ever-demanding industry. One of the challenges we need to overcome by bringing innovation to manufacturing is the proper industrialization phase followed by the appropriate standardization process and worldwide rollout in our facilities.
Few years ago, most of the eastern European automotive electronics production heavily employed human interaction, with manual and semi-automated processes; nowadays our products are built on fully automated robotic lines.
We invite you to join us on the road from Innovation to Standardization and get a glimpse of our manufacturing concepts based on the wholistic know-how approach of our worldwide technology networks.
Examples of applications developed according to the described methodologies will be presented as the common model being rolled out and lived around the world.
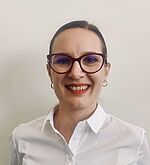
Educational mathematician and computer scientist, born in 1986, Laura Boarescu started her career in Continental Automotive Systems Sibiu 14 years ago as a production software engineer. For the past 10 years, she has led various production teams, especially in the software area. Laura specializes in helping different business areas to develop their people and products, from zero to success, from employee to leader, and that's why she is passionate about it. In her current position, Laura supports the definition and implementation of the business strategy in terms of new product launches, in strong alignment with the division's strategy. Its purpose in this process is to ensure constant inter-functional communication and cooperation in all reference stages of the project, from equipment specifications to delivery to series production. Laura strongly believes that there are always two important pillars: people and business and, by growing together, results in a valuable company culture, in which innovation, continuous improvement, high performance and collaboration are key factors for success.
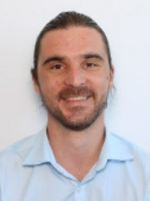
Born in 1985, Lucian Rusu is the Head of Digital Factory in Continental Automotive Systems Sibiu, leading change in areas of hardware and software development, from tangible mechanical elements and all the way to the cloud. Having more than 10 years of experience in IT, being a passionate coder and staying connected with the IoT world, he dedicated his last few years working on “the factory of the future” concept in Continental Sibiu. His passions are linked with everything that “flies, moves, speaks or see” in the robotics, IoT & AI world.
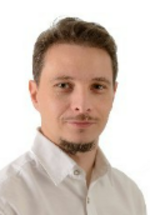
Born 1980, diploma in telecommunications at the Technical University of Cluj-Napoca, Romania.
He started with the international automotive supplier Continental AG in 2004. In his current position, Mr. Gruian is the head of Production Software Solutions within Automotive Manufacturing (AM) and has a strong test technologies background being a senior expert in this field. The Automotive Manufacturing is a cross-divisional organization within Continental Automotive Technologies Group, that includes dedicated central departments. His department, AM Digitalization & Technologies, is responsible for equipment software standardization, globalization of newly developed solutions, as well as piloting emerging technologies through specific innovation projects focused on manufacturing.
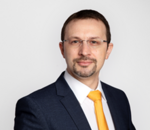
Born in 1981, graduated Technical University from Iasi, with diploma in Industrial Robots and Artificial Systems of View, Mr. Andrici started his career in automotive industry in 2005, joining the manufacturing production team in Continental Automotive Systems - Sibiu. During first years he had the chance to apply to the university studies in production, working with robots that automatically check optically or by X-Ray the quality of the Printed Circuited Boards Assemblies. For next year’s Sergiu took different leading positions for production teams or global projects, looking always for continuous improvement in both areas: people development and business performance. In his current position, as Head of Focus Factory ADAS, Sergiu is leading the autonomous mobility manufacturing business in Sibiu, with the mission to deliver the highest quality products to the customers within a sustainable and competitive business operation.
Sponsored Session 4 - The path towards Autonomous Mobility and the technologies that takes us there
Ovidiu Chicea
Alin Scortar
The world is constantly changing, and at the hearth of it autonomous mobility is constantly evolving. As a leading product supplier in the automotive industry, we focus on developing, delivering and validating state of the art technology.
Within this workshop, we want to present how we are actively shaping safety critical applications, and how easily we integrate in the vehicles of tomorrow but also in the vehicles of today.
We will focus on understanding the levels of automated driving and the technologies / products / functions that are making it possible.
A live demo from a vehicle equipment with ADAS sensors will be transmitted live. Based on this, a debate will be generated and will reveal the performance of various AM technologies depending on environmental conditions (weather conditions, visibility etc).
The purpose of the workshop is to cover the whole system, from AM sensors to braking systems, and a solution for one of the most critical topic within the Automotive industry: Safety.
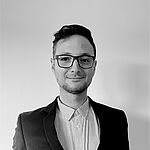
Hi! My name is Ovidiu and I have been working in Conti for more than 10 years now.
All this time, I had the opportunity to work with extraordinarily nice people from 4 departments.
I started in Transmission, where I learned about gearboxes and worked on developing control units for automatic gearboxes.
Later, I moved to Engine Systems where I worked with engine control units in collaboration with Transmission projects.
I spent the next 2 years in the Advanced Development team where I worked with a lot of new technologies and concepts, developing prototypes from idea to concept products.
For 3 years, I have been working in the ADAS (Advanced Driver Assistance Systems) department, where we have been working with various perception technologies such as Camera, Radar and Lidar to understand what is happening around a car, and how we can develop the next generation of functions that pave the road towards Automated Driving.
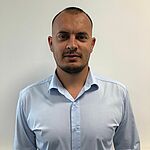
Hello! My name is Alin and I have been working in Continental for 10 years.
In this time period, I worked in Electronics discipline of the Braking department. In the first 4 years, I had a technical responsibility in hardware testing and for the last 6 years I switched to the hardware discipline project management. My main responsibility is to foster the braking ECUs from quotation phase to your vehicles.